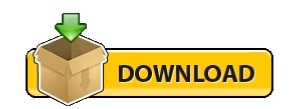

The printing of parts and products has the potential to transform manufacturing because it lowers the costs and risks. It can be printed in nylon, stainless steel or titanium. The printers can also produce ready-made objects that require less assembly and things that traditional methods would struggle with-such as the glove pictured above, made by Within Technologies, a London company.
#3d printer prototype software#
The additive process requires less raw material and, because software drives 3D printers, each item can be made differently without costly retooling. Using 3D printers as production tools has become known in industry as “additive” manufacturing (as opposed to the old, “subtractive” business of cutting, drilling and bashing metal). He predicts that this will rise to 50% by 2020. More than 20% of the output of 3D printers is now final products rather than prototypes, according to Terry Wohlers, who runs a research firm specialising in the field. As 3D printers have become more capable and able to work with a broader range of materials, including production-grade plastics and metals, the machines are increasingly being used to make final products too. It started ticking.Įngineers and designers have been using 3D printers for more than a decade, but mostly to make prototypes quickly and cheaply before they embark on the expensive business of tooling up a factory to produce the real thing. It took him a few attempts to get right, but eventually he removed the plastic clock from a 3D printer, hung it on the wall and pulled down the counterweight. At the Massachusetts Institute of Technology (MIT), Peter Schmitt, a PhD student, has been printing something that resembles the workings of a grandfather clock. These include medical implants, jewellery, football boots designed for individual feet, lampshades, racing-car parts, solid-state batteries and customised mobile phones. The researchers at Filton have a much bigger ambition: to print the entire wing of an airliner.įar-fetched as this may seem, many other people are using three-dimensional printing technology to create similarly remarkable things.
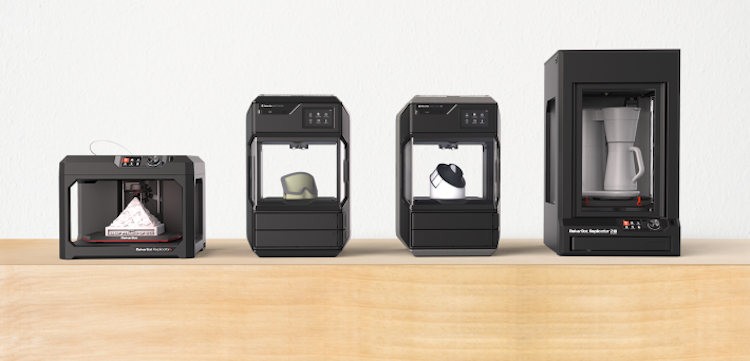
Little by little a machine is “printing” a complex titanium landing-gear bracket, about the size of a shoe, which normally would have to be laboriously hewn from a solid block of metal. In a building near a wind tunnel on the same sprawling site, something even more remarkable is being created. FILTON, just outside Bristol, is where Britain's fleet of Concorde supersonic airliners was built.
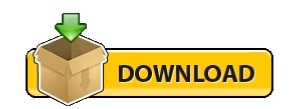